- Home
- >
- Products
- >
- Stone Processing Equipment and Diamond Tools
- >
- Sintered Diamond CNC Stubbing Wheel for Stone Slab Calibration
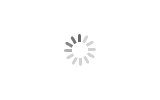
Sintered Diamond CNC Stubbing Wheel for Stone Slab Calibration
Product origin :China
CAFU's high-quality Sintered Diamond CNC Stubbing Wheel is one of the preferred diamond tools for stone processing. Our Stubbing Wheels are meticulously designed to deliver exceptional performance in processing marble, granite, engineered stone, and more. Leveraging high-grade synthetic diamonds and top-quality raw materials, we provide customized solutions to create the most durable, safe, and reliable diamond tools for your specific needs.
Sintered Diamond CNC Stubbing Wheel for Stone Slab Calibration - CAFU Custom Solutions
Product Highlights
Customization Capability
At CAFU, customization is at the core of what we do. Whether you require Stubbing Wheels for rough machining or fine polishing, we can tailor - make a full range of diamond tools with various grit sizes based on your processing precision. Our team of diamond tool process engineers, with over 20 years of experience and a track record of supplying to numerous stone processing manufacturers worldwide, can handle every detail. From matrix design, Sintered process design, welding technology, to cooling process design during cutting and chip removal design, we provide professional design knowledge and comprehensive system - level solutions.
High - Quality Materials
We use high - grade synthetic diamonds and premium raw materials in manufacturing our Stubbing Wheels. This ensures that our tools are not only durable but also capable of delivering consistent and high - quality results in stone slab calibration.
Superior Performance
●Wear Resistance: CAFU's CNC stone processing tools, especially our Stubbing Wheels, are highly resistant to wear, allowing for long - term use and reducing the frequency of tool replacement.
●Excellent Dynamic Balance: Every Stubbing Wheel undergoes thorough inspection and correction for dynamic balance. This ensures smooth operation, reduced vibration, and enhanced safety during CNC machining.
●Strong Welding: The welding of diamond segments on our Stubbing Wheels is robust, ensuring that the segments stay in place even under intense cutting forces.
●Lower Total Cost of Ownership: With long service life, reduced downtime for tool changes, and reliable performance, our Stubbing Wheels help you achieve a lower total cost of ownership in the long run.
Product Specifications
Item No. | Outer Diameter (mm) | Segment Height (mm) | Thread Size(mm) | Type |
5020 | 50 | 20 | 10 | Segmented |
8620 | 86 | 20 | 50 | |
8630 | 86 | 30 | ||
10020 | 100 | 20 | ||
10030 | 100 | 30 | ||
9020 | 90 | 20 | 50 | Continuous |
9030 | 90 | 30 | ||
10020 | 100 | 20 | ||
10030 | 100 | 30 |
Note: The above specifications are for reference only. Customization is available to meet your specific requirements.
Application
Our Sintered Diamond CNC Stubbing Wheels are suitable for CNC machines. They support connection methods including Ø35, Ø22, and 1/2"G. Ideal for processing various stones such as marble, granite, and engineered stone, these Stubbing Wheels can be customized for different machining stages from roughing to fine polishing.
Why Choose CAFU?
CAFU stands out as a preferred choice for CNC diamond tools. Our Stubbing Wheels are a testament to our commitment to quality, customization, and performance. With decades of experience in the field, our process engineers can provide you with the most suitable and reliable diamond tool solutions. Whether you are a large - scale stone processing factory or a small - batch producer, we have the expertise and capability to meet your needs.
Invest in CAFU's Sintered Diamond CNC Stubbing Wheels for your stone slab calibration needs and experience the difference in quality, durability, and performance. Contact us today to discuss your custom Stubbing Wheel requirements and take your stone processing to the next level.
Customized design of general fabricated steel silo needs to provide: 1. Storage material name 2. Density of storage material 3. Storage material particle size 4. Storage capacity 5. Feeding method 6. Discharge method and size of discharge port 7. The height of the discharge port from the ground...more