- Home
- >
- Products
- >
- Stone Processing Equipment and Diamond Tools
- >
- Sintered Diamond Milling Wheels for Bridge Saws and CNC
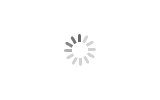
Sintered Diamond Milling Wheels for Bridge Saws and CNC
Product origin :China
In the field of stone processing, achieving precise thickness control and excellent surface finishing is crucial for meeting the stringent requirements of construction and decoration projects. The Sintered Diamond Calibrating Wheel emerges as a solution for precise rough - blank processing of stone, designed to deliver outstanding performance in stone thickness adjustment.
Sintered Diamond Calibrating Wheel: Precision Tool for Stone Processing
Core Functions
1. Precise Thickness Control
The Sintered Diamond Calibrating Wheel is engineered to provide highly accurate thickness control during stone processing. Whether you are working on granite, marble, or artificial stone, this tool ensures that the final product meets the exact thickness specifications, laying a solid foundation for high - quality construction and decorative applications.
2. Optimized Surface Treatment
Beyond just thickness adjustment, it plays a vital role in optimizing the surface of the stone. The wheel's design and the properties of the sintered diamond ensure that the processed stone surface is smooth and free from defects, enhancing the aesthetic appeal and value of the stone products.
3. Stable and Efficient Operation
Featuring a dynamic balance design, the calibrating wheel operates with low vibration. This not only ensures stability during high - speed rotation but also contributes to an improved processing efficiency. By reducing unnecessary vibrations, the tool can work more smoothly, shortening the overall operation cycle and increasing productivity. Additionally, some types (like the nylon - core form) offer excellent noise - reduction effects, creating a more comfortable working environment.
Main Types
1. Full Steel Matrix Type
Composed of a high - strength steel matrix and sintered diamond wear - resistant alloy segments, which are combined through copper welding. This integral structure is simple and robust. However, it has a limitation in terms of noise insulation. During the stone grinding process, it tends to generate relatively large noise, making it more suitable for stone processing sites where there are no strict noise requirements in the surrounding area. In such cases, workers must wear earplugs to protect their health from the noise.
2. Nylon Core Type (Silent Structure Design)
This type consists of a Teflon Core and a steel matrix, assembled together with high - strength bolts. Compared to the full steel matrix type, the processing technology of the Teflon Core + steel matrix combination is more complex to ensure high reliability. But this complexity brings about a significant advantage – a much higher mute effect.
The processing steps for this type are as follows:
● Rough Machining of Outer - ring Steel Blank: A machining allowance must be reserved, and finish turning is carried out after the welding process to ensure the best dynamic balance performance.
● Sandblasting of Welding Surfaces: All welding surfaces are sandblasted to enhance the welding strength and ensure the welding quality.
● Finish Machining of the Rough Blank: To achieve the required precision.
● Assembly with Teflon Core: Bringing together the different components.
● Edge - opening Treatment of Diamond Tips: According to the rotation direction, the surface of the sintered diamond is opened to ensure a good grinding effect during use.
● Overall Dynamic Balance Testing and Adjustment of the Diamond Milling Wheel: High - quality processing technology usually results in very few dynamic balance compensation holes, reducing the secondary processing of the milling wheel body caused by a large number of compensation hole operations.
Applicable Machines and Connection Methods
The Sintered Diamond Calibrating Wheel is applicable to Edge Cutting Machines and Bridge Cutting Machines. The connection methods are Ø50/Ø60, ensuring compatibility with a wide range of equipment in the stone processing industry.
Tooth - shape Arrangement
In general, an oblique - tooth arrangement design is adopted. This design facilitates better chip removal during the stone grinding process, improving the overall processing efficiency and the quality of the processed surface. However, for milling wheels with short teeth, a flat - tooth structure may be used according to process requirements.
Specification Parameters
We offer two main series of calibrating wheels with the following specifications:
1. Oblique Segment Calibrating Wheel
Item No. | Outer Diameter (Inch) | Outer Diameter (mm) | Segment Length (mm) |
12(14) - 20 | 12/14 | 300/350 | 20 |
12(14) - 25 | 12/14 | 300/350 | 25 |
12(14) - 30 | 12/14 | 300/350 | 30 |
12(14) - 35 | 12/14 | 300/350 | 35 |
12(14) - 40 | 12/14 | 300/350 | 40 |
12(14) - 50 | 12/14 | 300/350 | 50 |
Other sizes: Customizable
2. Silent Calibrating Wheel
Item No. | Outer Diameter (Inch) | Outer Diameter (mm) | Segment Length (mm) |
S14(16) - 20 | 14/16 | 350/400 | 20 |
S14(16) - 25 | 14/16 | 350/400 | 25 |
S14(16) - 30 | 14/16 | 350/400 | 30 |
S14(16) - 35 | 14/16 | 350/400 | 35 |
S14(16) - 40 | 14/16 | 350/400 | 40 |
S14(16) - 50 | 14/16 | 350/400 | 50 |
Other sizes: Customizable
CAFU Machinery's Sintered Diamond Calibrating Wheel is crafted from high - quality raw materials. It features a technological design that combines wear resistance and sharpness, making it an excellent choice when you are selecting diamond tools for stone processing. Our unique and innovative sintered diamond tool formula is suitable for processing high - hardness granite, easy - to - crack marble, artificial stone, and more. Contact our sales manager at any time, and we will provide you with the best diamond tool solution for your Sintered Diamond Calibrating Wheel needs.
Customized design of general fabricated steel silo needs to provide: 1. Storage material name 2. Density of storage material 3. Storage material particle size 4. Storage capacity 5. Feeding method 6. Discharge method and size of discharge port 7. The height of the discharge port from the ground...more