- Home
- >
- Products
- >
- Building Materials Machinery
- >
- High Efficiency Ribbon Blenders and Mixers
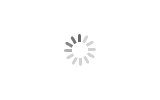
High Efficiency Ribbon Blenders and Mixers
Product origin :China
The ribbon blenders and mixers supplied by our company feature a large loading coefficient (minimum 70%), high mixing uniformity, and excellent shaft end sealing performance (constant pressure mechanical seal). They are applicable to a wide range of materials and widely used in industries such as building materials and new materials, metallurgy and mining, environmental protection and waste treatment, and chemical and fine chemical industries. They can fully meet the high-end requirements for efficient mixing of powder with powder, powder with a small amount of liquid, and powder with granules.
Our Industrial Ribbon Mixers and Ribbon Blenders are particularly suitable for applications requiring excellent stable working conditions and extremely high mixing uniformity.

Excellent Double Ribbon Design
The double ribbon adopts an interrupted design, ensuring mixing uniformity while consuming less power. A reasonably designed double ribbon mixer can ensure efficient material mixing and stirring in the innovative integral "U" - shaped mixing chamber, enabling full mixing of various materials. According to the requirements of different materials, the surface of the double ribbon can also be custom - sprayed with tungsten carbide or zirconia ceramics to improve the overall service life of the double ribbon mixer. The stirring main shaft is flange - connected with the transmission shafts at both ends, which is particularly suitable for later maintenance.
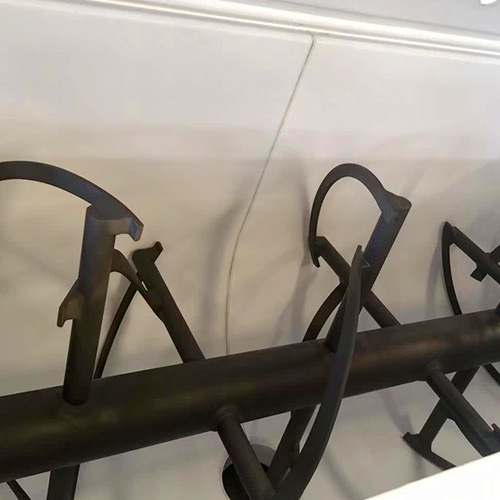
Customization High - Quality Mixing Chamber
The material contact surface of the mixing chamber of the ribbon mixer can be made of 316L, 321, 304, or carbon steel (the entire ribbon blenders can be made of stainless steel) as required. The surface of the integral "U" - shaped mixing chamber can be lined with high - quality PTFE to reduce material adhesion to the chamber wall and achieve fine mixing of materials.
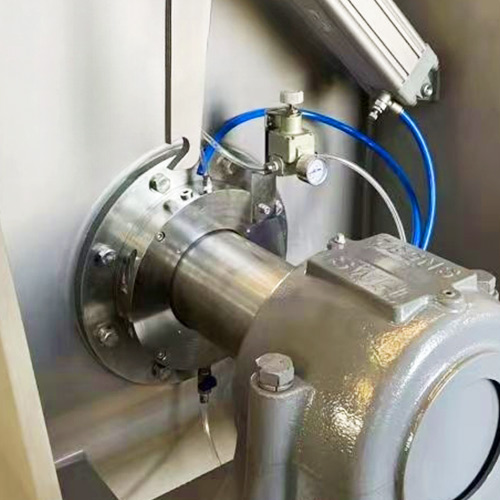
High - Grade Shaft End Sealing Performance
The shaft end seal of the ribbon blender machine is standard - matched with a high - quality mechanical seal, which has excellent sealing performance, reliable and stable long - term use, and basically prevents dust or materials from overflowing through the shaft end.
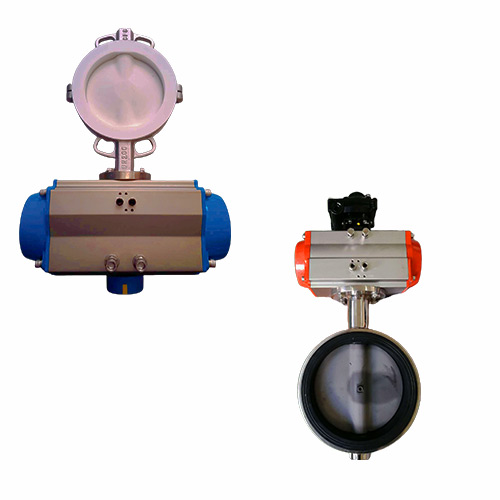
High - Performance Optional Accessories
Optional full PTFE pneumatic butterfly valves or tungsten carbide - sprayed discharge valves.
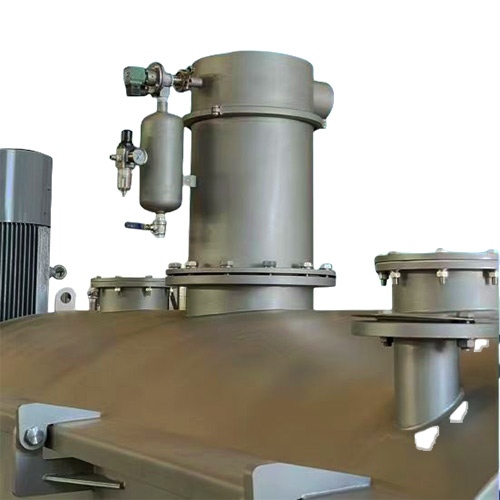
High-Efficiency Filter Element Equipped Air Backblowing Purification Device
An air backblowing purification device with a high-efficiency filter element can effectively handle the dust generated during the mixing process, purify the exhaust gas, prevent dust from leaking out, and maintain the pressure balance inside the equipment.
Main Technical Parameters
● Processing Capacity: 0.1m³ - 30m³
● Mixing Time: 3 - 15 minutes
● Equipment Material: 316L, 321, 304, carbon steel
● Drive Device: Explosion - proof motor, variable frequency motor
● Discharging Device: Pneumatic butterfly valve, pneumatic curved flap valve, rotary feeding valve, etc.
● Opening Method: Full - open or other types. The feed inlet can be customized according to the process.
● Auxiliary Components: Customized according to the process
Supporting Equipment Solutions for High Efficiency Ribbon Blenders and Mixers
Main Applications of Ribbon Blenders and Mixers
● Building Materials and New Materials Industry: Dry mortar mixing, ceramic and refractory materials, dry premixing of battery materials
● Metallurgy and Mining Industry: Metal powder mixing, mineral powder and reagent mixing
● Environmental Protection and Waste Treatment Industry: Mixing of sludge and conditioner, resource regeneration of solid waste
CAFU Machinery is proficient in the conveying, crushing and screening, mixing of various bulk solid materials such as building materials and new materials. If you have any industrial ribbon mixer and ribbon blenders projects that need consultation, please feel free to contact our service team.
Customized design of general fabricated steel silo needs to provide: 1. Storage material name 2. Density of storage material 3. Storage material particle size 4. Storage capacity 5. Feeding method 6. Discharge method and size of discharge port 7. The height of the discharge port from the ground...more